

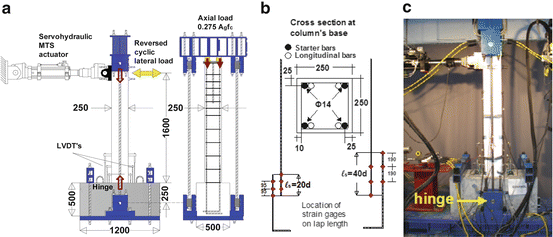
Committee 318 considered suggestions from many sources, including ACI Committee 408, but has retained a two-level splice length primarily to encourage designers to splice bars at points of minimum stress and to stagger splices to improve behavior of critical details.ġ2.15.2 - Lap splices of deformed bars and deformed wire in tension shall be Class B splices except that Class A splices are allowed when: Thus, the Class C splice was eliminated although development lengths, on which splice lengths are based, have in some cases increased.
#Aci class b lap splice code#
The 1989 code contained several changes in development length in tension that eliminated many of the concerns regarding tension splices due to closely spaced bars with minimal cover. For staggered splices, the clear spacing is taken as the minimum distance between adjacent splices. R12.15.1(a) illustrates the clear spacing to be used. For splices in columns with offset bars, Fig. When multiple bars located in the same plane are spliced at the same section, the clear spacing is the minimum clear distance between the adjacent splices. The development length ld used to obtain lap length should be based on fy because the splice classifications already reflect any excess reinforcement at the splice location therefore, the factor from 12.2.5 for excess As should not be used. R12.15.1 - Lap splices in tension are classified as Type A or B, with length of lap a multiple of the tensile development length 1d. Where ld is calculated in accordance with 12.2 to develop fy without the modification factor of 12.2.5. R12.15 - Splices of deformed bars and deformed wire in tensionġ2.15.1 - Minimum length of lap for tension lap splices shall be as required for Class A or B splice, but not less than 12 in., where: 5 bars and smaller due to the potentially brittle nature of failure at these welds. The 1995 code limited these lower strength welds and connections to No. Therefore, lap welds of reinforcing bars, either with or without backup material, welds to plate connections, and end-bearing splices are allowed under certain conditions. R12.14.3.5 - The use of mechanical or welded splices of less strength than 125 percent of specified yield strength is permitted if the minimum design criteria of 12.15.4 are met. The 1995 code eliminated a requirement that the bars be butted since indirect butt welds are permitted by ANSI/AWS D1.4, although ANSI/AWS D1.4 does indicate that wherever practical, direct butt splices are preferable for No. See the discussion on strength in R12.14.3.2. The tensile strength requirement of 125 percent of specified yield strength is intended to provide sound welding that is also adequate for compression.
#Aci class b lap splice full#
I want to have all my ducks in a row.R12.14.3.4 - A full welded splice is primarily intended for large bars (No. I checked the strength using the reduced capacity of section 12.2.5 and it works, but is this allowed at a splice location? Are the requirements of 12.2.5 just for straight development length? I have always allowed for reduced capacity of bars at lap splices, but this project might go to the courts. The pier experiences minor uplift and the reinforcement specified is complete overkill(designed by others). I am reviewing a project for a client of ours (we didn't do the design for this project) and the dowels for the pier reinforcement only have a splice of around 16". The commentary under 12.15.1 states "The development length ld used to obtain lap length should be based on fy because the splice classifications already reflect any excess reinforcement at the splice location therefore the factor from 12.2.5 for excess As should not be used". Linear reduction in the capacity based on the reduced development length. The modification factor in 12.2.5 is the As provided/ As req'd reduction. In Section 12.15.1 in the notes under the splice requirements of 1.3(ld) for Class B splices it states, "where ld is calculated in accordance with 12.2 to develop fy without the modification factor of 12.2.5".
